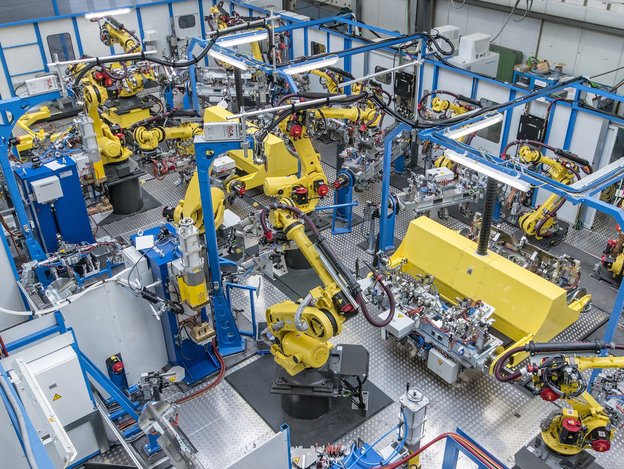
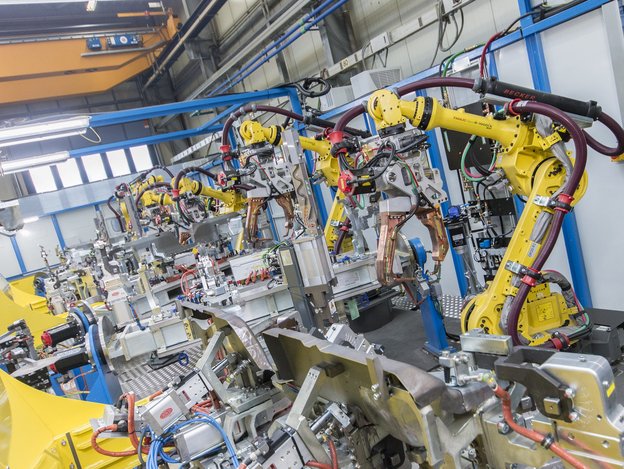
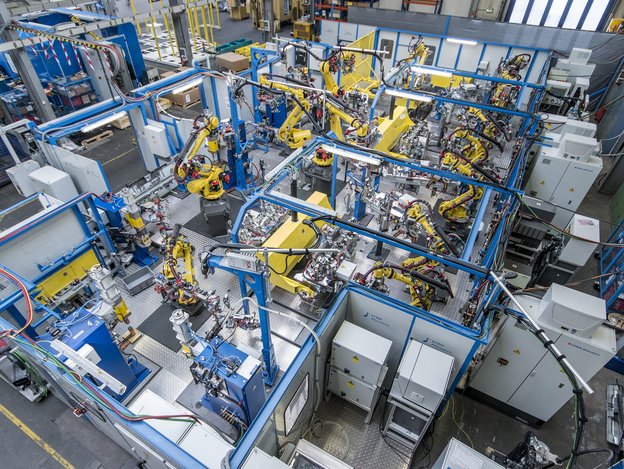
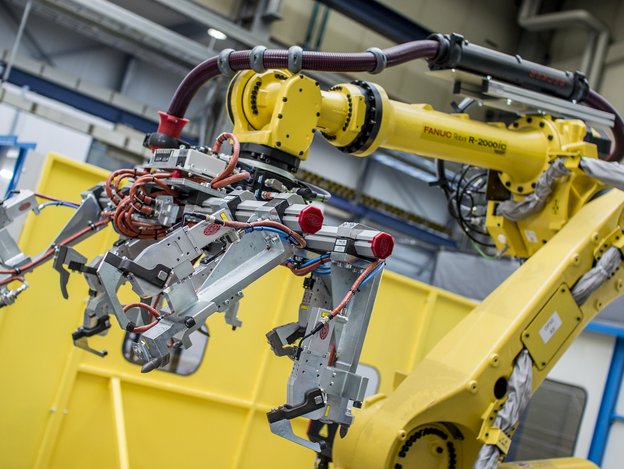
System layout
Profound German Engineering
All over the world, automotive body-in-white manufacturers in particular rely on the top performance of our TURNKEY joining systems. "Mastering the beast." In the conception, in the complete penetration of the system, we generate decided advantages. In every process step, we turn up the performance screw. The plant layout is not about stringing components together. It is about answering many questions: How can I accelerate each individual work step of the cell? How do I safeguard the process and ensure maximum up time? Which processes do I use? And how do I achieve the highest degree of automation with a minimum of personnel? The magic word is engineering. The perfect interplay of experience, know-how, specialists and technology. Add to this our SpeedLine products and we are setting standards in the market.
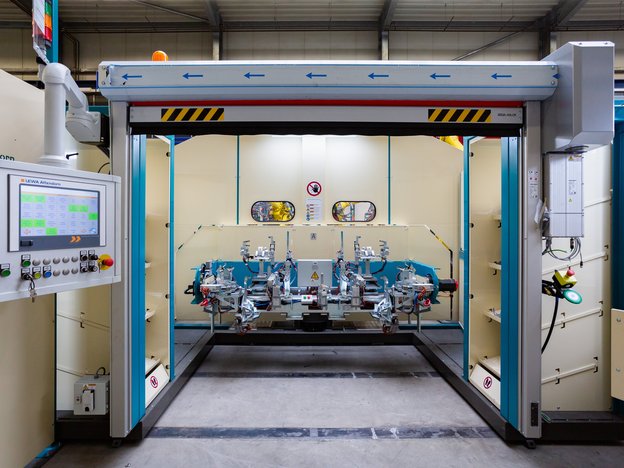
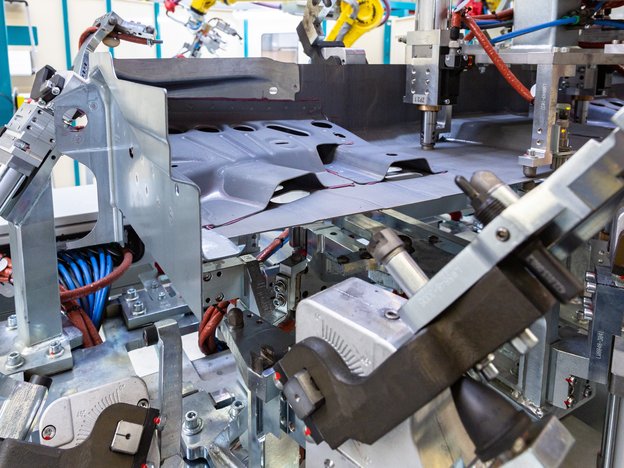
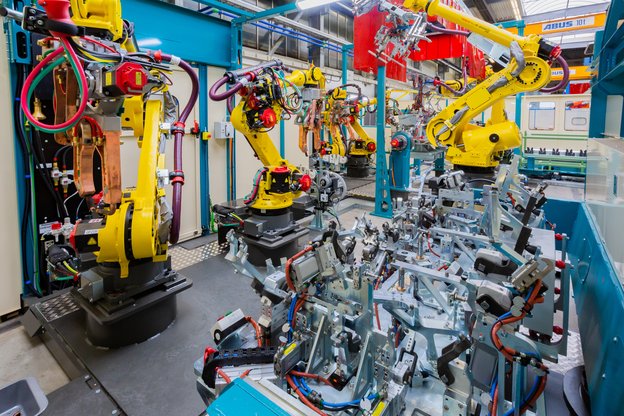
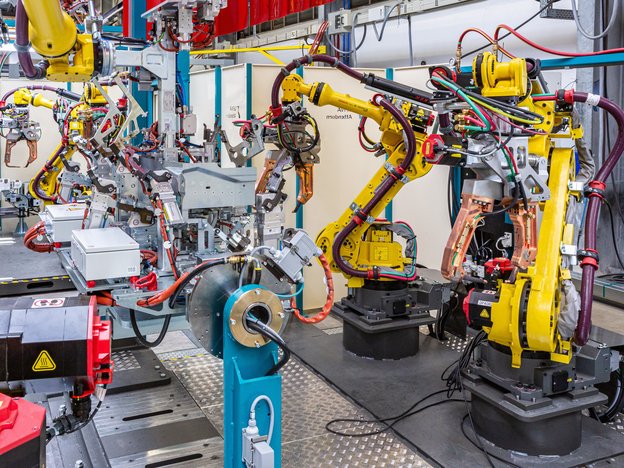
Efficient assembly production
Focus Automotive
As an OEM or Tier1 supplier, you need to manufacture assemblies quickly and reliably. To this end, we offer reliable joining processes for all materials used today, and ensure speed, availability and complete traceability. Inour history, we have put more than 2,250 automated joining systems into operation worldwide, some with a project volume of up to € 20 million. Our systems are used to manufacture almost all body-in-white structural parts. We also solve complex joining tasks and have been involved in the topic of e-mobility since 2012. We know the challenges of the automotive industry and see ourselves as a partner who provides unique solutions to complex challenges.
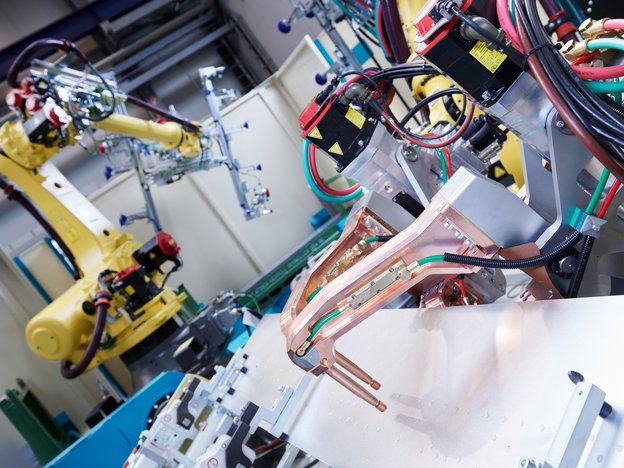
Patch board welding
Ready for electromobility
In modern lightweight construction, with regard to weight savings in electric vehicles, raw blanks made of high-strength steels are increasingly being doubled. This is a demanding process that we have already implemented several times using fast, fully automated patch blank welding.
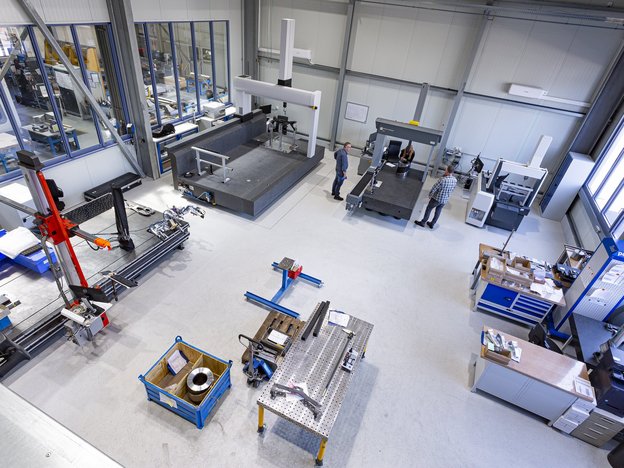
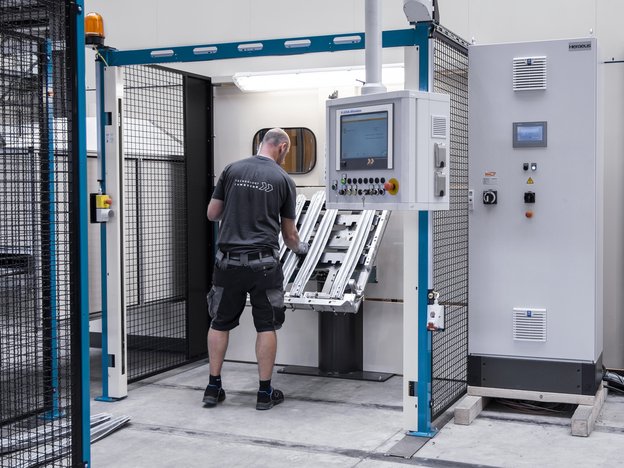
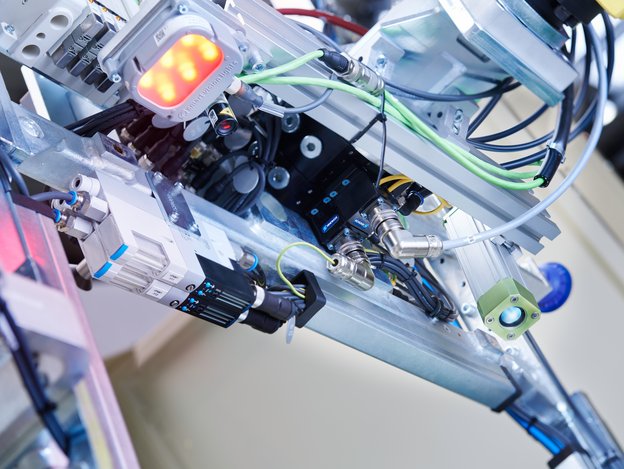
Quality
Completely continuous
Our quality management system (according to DIN EN ISO 9001:2015) is not only implemented throughout the organizaion, we live it daily. Nothing comes into our house, nothing leaves our house, which does not meet our very high quality standards. Quality has several meanings for us. First of all, it concerns the products that we manufacture and the cells that we develop, build and commission for you. It is also about the traceable quality of the products you manufacture with our systems. Only because we think and implement quality from A to Z and beyond our factory gates can we offer you the reliability and longevity of our automated joining systems and give you a competitive edge.
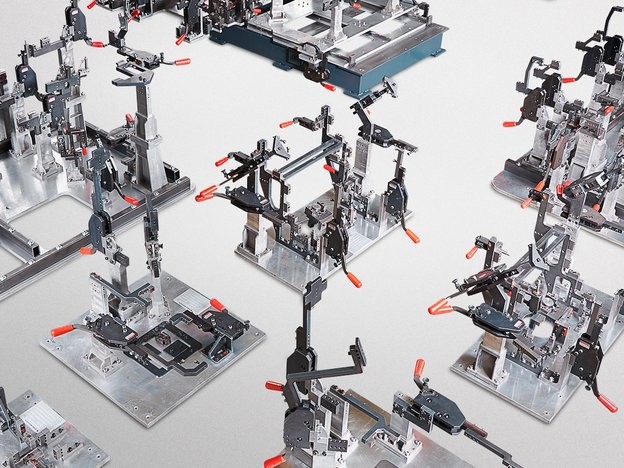
Prototypes & Pre-series
First products
Once the system has been set up and adjusted with all modules and components, we can produce prototypes or high-quality, reproducible pre-series components for you. This gives you the opportunity to coordinate and evaluate parts with customers at an early stage.
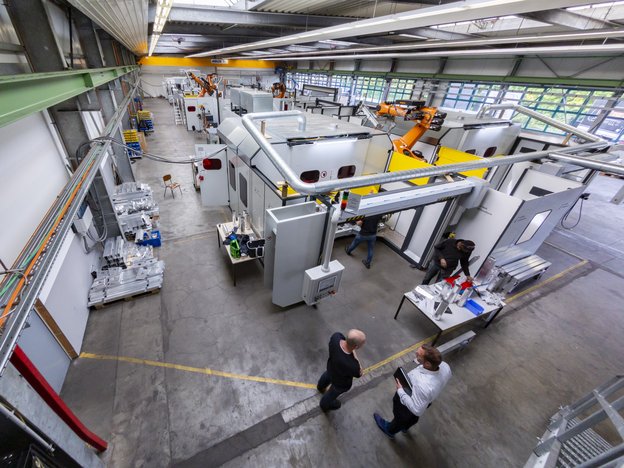
Assembly
Professional assembly
For us, dismantling the system manufactured by us and packing it cleverly means being prepared for the assembly and installation in detail. Nothing is missing, everything has its place and we know exactly what goes where. Of course, coordinated with your site and infrastructure.
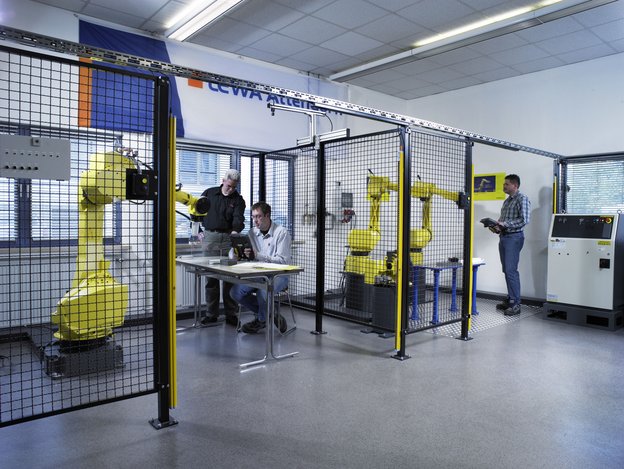
Trainings & courses
Transfer of know-how into practice
We want you to be able to use and access the full performance as well as the full potential built into our systems and the components used. With training & education, we show you how to operate the systems safely and efficiently. Our course program is modular and ranges from introductory courses to expert courses and customer-specific training.